World Class Palletizing System
The Client & Objective
As the largest food processing company in the United States, our client was looking for an improvement over its current manual processes with smart, digital solutions throughout its vast operation. Having already earned a solid reputation by solving a complex palletizing problem for one if its processing plants, MMCI was up for this next challenge.
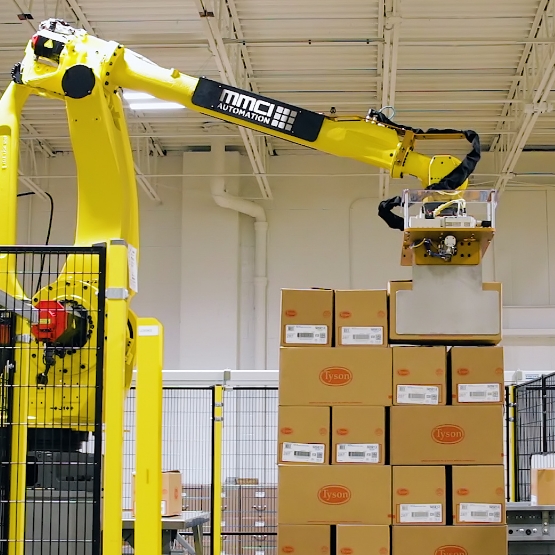
The Challenge
In a nutshell, the challenge presented to MMCI was to analyze every aspect of a robotic case palletizing system to see if it could be made faster, more consistent, reliable, safer, smaller, smarter, more versatile, and easier to operate and maintain. In other words, "Create a world class palletizing system to reflect our needs and future growth."
The Solution
Tapping into the knowledge and experience of our entire team - from the design engineers and conveyor experts to our in-house controls and robotics specialists - we set out to improve on every aspect of a typical robotic palletizer.
1. Faster
To make it faster, we designed the system's inbound conveyors with sensors that would not only ensure proper sealing and alignment, but track over 80 data points that would feed two separate robotic arms, staging tables and a discharge conveyor for out-of-spec cases.
Our design team also studied the average size of each case, pallet heights and other critical factors to determine the optimal height to place the incoming conveyors, robotic arms and pallets.
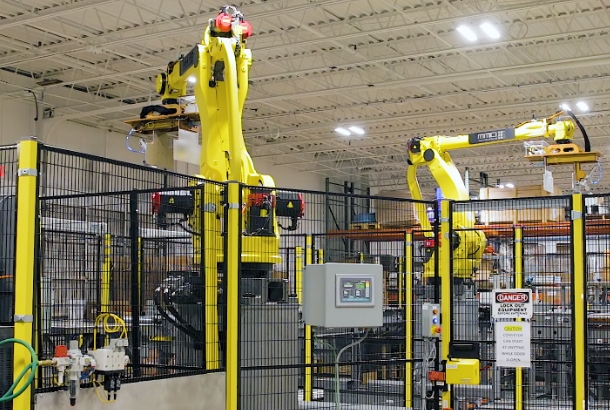
Reduced Travel Time
While incremental in nature, the reduced movement required when compounded over hundreds of thousands of cases led to a substantial improvement in productivity and throughput as well as reducing the demands on the robot.
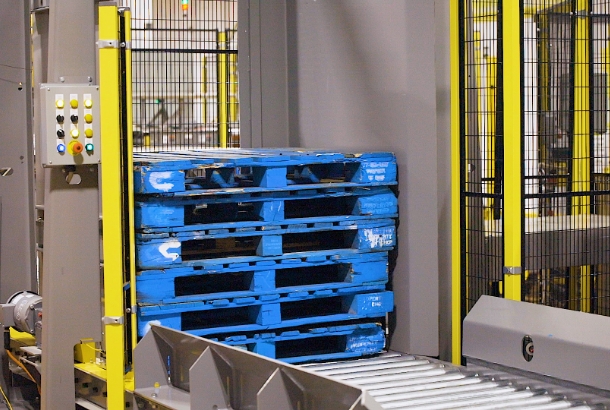
Automatic Pallet Dispensing
To automate the pallet dispensing process and minimize the frequency in which the dispenser needed to be filled, we outfitted the cell with a heavy-duty pallet dispenser featuring an added staging position. This "simple" enhancement not only improved efficiency, but improved safety by reducing forklift traffic near the cell.
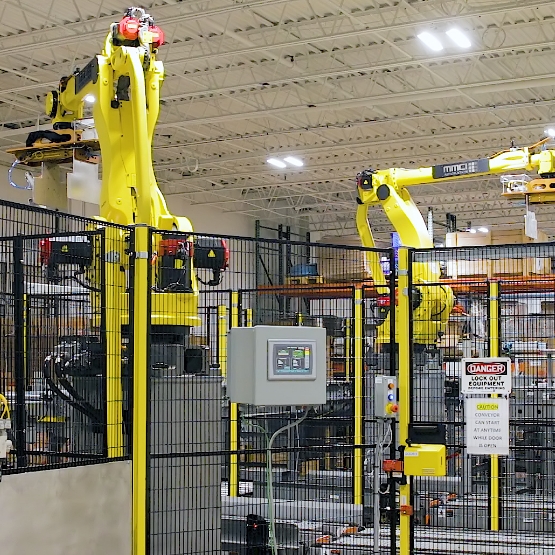
2. Safer
In addition to all of the standard safety features, we utilized 24-volt infeed conveyors that are safer for workers hands and fingers and safety-rated valves to remove pressure from the clamping system.
Safety Controllers
We also used safety-programmable controllers from Allen Bradley that allow standard and safety-related programs to reside in a single controller chassis - providing flexibility in programming as well as a familiar and easy-to-use environment for programmers.
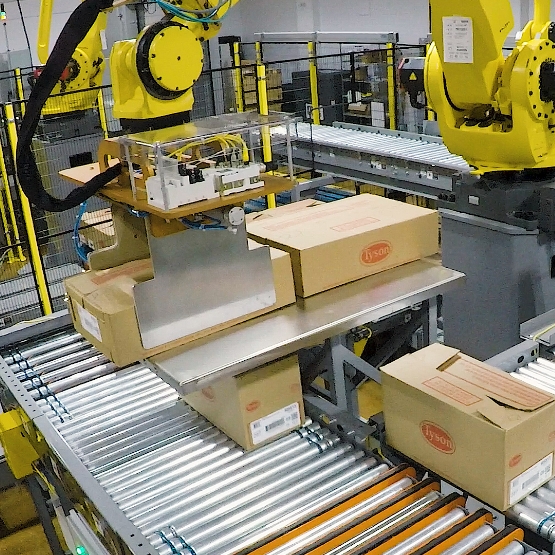
3. Smaller
To make it smaller, our design team drew upon its world class extensive experience in conveying technology and pallet dispensing to minimize the footprint of the system.
Efficient Design
We started by consolidating all cases through one inbound conveyor outfitted with sensors and controls that would determine its next path. We then took advantage of the inbound conveyor's height, to install two pallet transfer stations below the incoming conveyor. From here, we directed pallets to the palletizing area and then consolidated the full pallets back to one outbound conveyor which would be outfitted with an inline stretch-wrapper.
Sensors, controls, staging tables and accumulation conveyors were utilized throughout the entire cell to ensure maximum productivity in this small area.
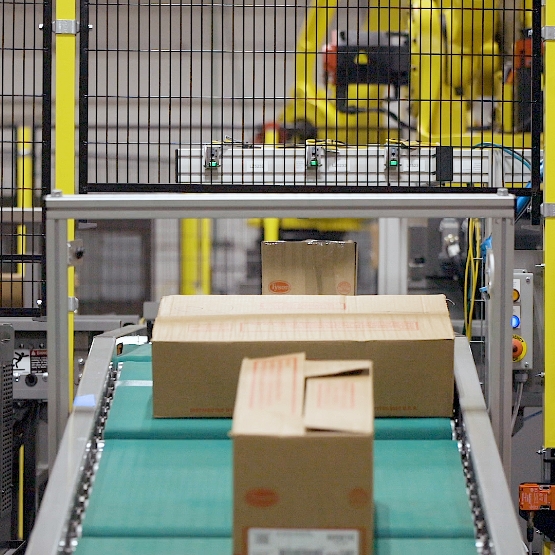
4. Smarter
To make the system smarter, our controls team integrated a variety of specialized sensors that not only checked the case for proper sealing, alignment and label quality, but also captured over 80 identifiers while the product was in motion that aided in operation and tracking.
Not only were damaged or improperly sealed or labeled cases automatically directed towards a discharge conveyor for inspection and re-work, but information on all packages, cases and pallets was captured and stored.
Some of this data was then utilized by the custom-designed HMI that provided operators with real-time information helpful in maximizing productivity, quality and safety.
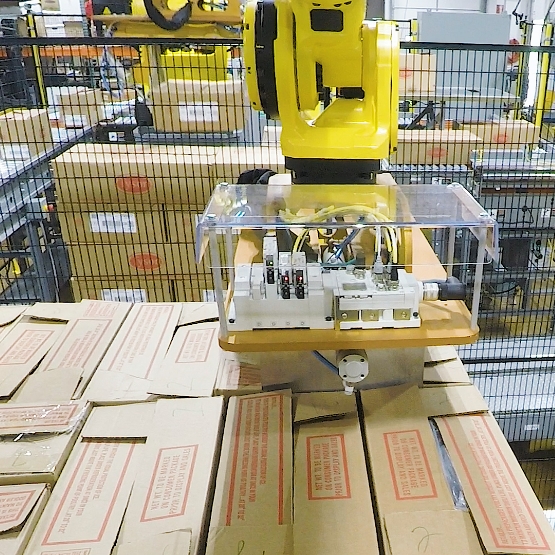
5. More Versatile
We designed the system to be as versatile as possible - knowing that it may need to accommodate many case sizes and adjust quickly to line changeovers.
The similarity of case sizes allowed us to utilize a proven end-of-arm tooling design, but we noticed during line changeovers that more than two unique cases were being fed into the cell. To rectify this situation without slowing the system or rejecting the cases, we integrated staging tables where the robot could temporarily place cases until the existing pallet was complete.
6. Easier to Operate and Maintain
To further ensure exceptional performance, our team developed systems and controls to monitor the entire system and its 10 major elements with easy-to-navigate screens for each section of the palletizing system.
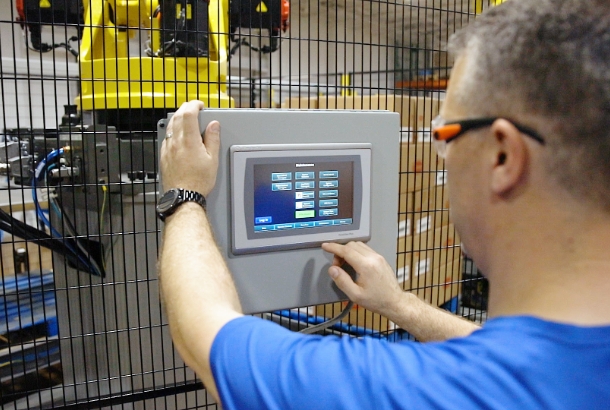
Intuitive HMI
Through the intuitively-designed HMI, operators can monitor and control every aspect of the system from a safe area next to the cell.
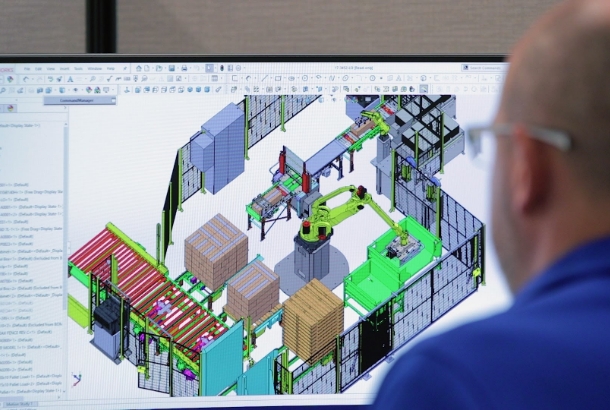
Offsite Support
If, by some reason, an operator runs into challenges he cannot solve, the system can be placed into VPN mode so MMCI Automation team members can log into the system remotely and address the issue.
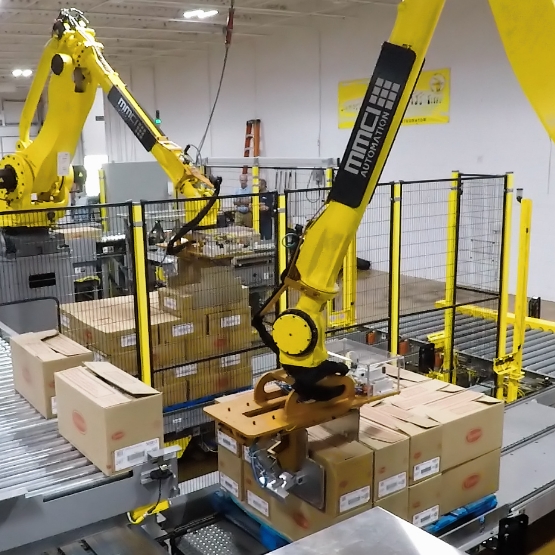
The Result
After testing the system in our own Robotics and Automation Technology Center, we felt confident that we had successfully designed another world-class palletizing solution for our customer.
World Class System
Upon completion of testing, the cell will be shipped and set-up by our experienced field installation team at our client's Manufacturing & Automation Technology Center where teams will be trained on its operation so that it can be deployed nationwide.