Robotic vs. Conventional PalletizersWhich is Right for You?
Historically speaking, you had to choose between conventional palletizers for their speed or robotic palletizers for their flexibility, but you could not have both.
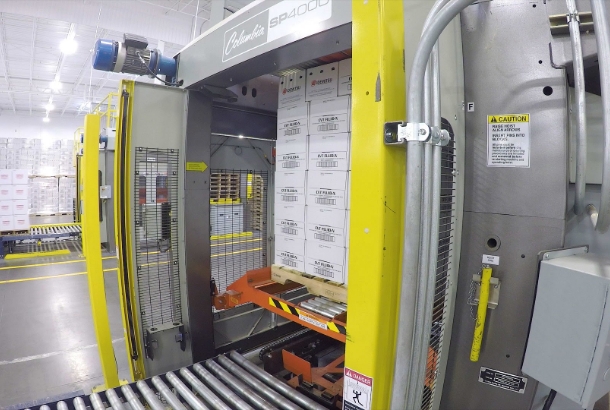
Conventional
Conventional palletizers have typically been specified for operations packing a single SKU at very high rates.
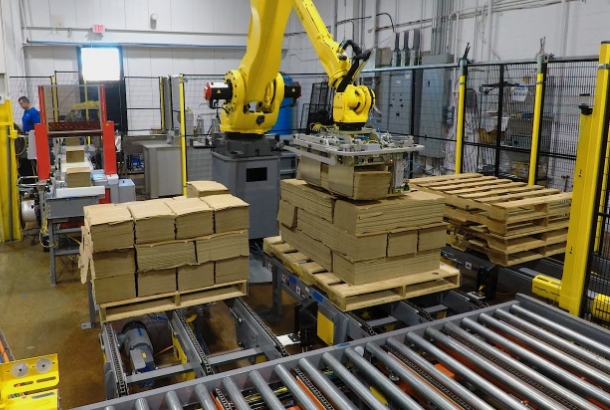
Robotic
Robotic palletizers have typically been specified for operations requiring a high level of flexibility.
At MMCI Robotics, we are closing the gap between the speed of conventional palletizers and robotic palletizers so you no longer have to sacrifice speed for flexibility.
Conventional vs. Robotic
Allow MMCI to help you specify the right palletizer system for your operation.
Conventional
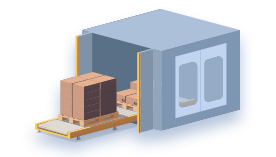
Robotic
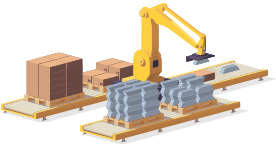
Applications
What are you palletizing?

- Designed for a single SKU
- Suitable for boxes, bags (cubed shaped)

- Designed for single or multiple SKUs
- Suitable for boxes, bags, pails, ingots, bottles, drums, bundles, bails or just about anything
Versatility
How many different products, sizes and pallet configurations?

- Limited versatility
- Conventional palletizers are designed to palletize one product type at a time

- Highly versatile
- Clamps, vacuum cups, forks and fingers on interchangeable end effectors can be adapted to many scenarios
Speed
How fast do you need to palletize and where are bottlenecks?

- Cases: up to 150/min
- Bags: between 10 and 40/min
- High-level palletizers allow products to be formed into layers at much higher speeds than low-level palletizers

- Cases: up to 30/min, but can be increased dramatically by picking rows
- Bags: up to 40/min
- Can handle a wider variety of skus and product shapes and pallet patterns
Productivity
Consider the productivity of the entire system, not just the palletizer.

- A conventional palletizer can often build pallets faster, but may be limited to bottlenecks elsewhere

- A jointed-arm robot can build four simultaneous pallet loads within its work cell
Costs
Initial investment, operating costs, maintenance, training?

- Initial costs: similar to robotic
- Higher operating costs as machines are powered by gear motors.
- Higher energy costs

- Initial costs: similar to conventional
- Typically requires less upstream conveyor than conventional palletizers
- Lower energy costs
Footprint
How much space is available and how is it configured?

- Conventional palletizers and their required conveyor systems typically occupy a greater amount of floor space

- Robots are an option where floor space is at a premium
Downtime
How badly will downtime affect your operation?

- More moving parts leads to more frequent downtime

- Low maintenance requirements keeps downtime to a minimum
Maintenance
Do you have a team in place?

- Requires more preventative maintenance but less specialized training

- More reliable, significantly less downtime, requiring less maintenance
Training
How easy are systems to operate and maintain?

- Conventional palletizers operate on the same control platform as other equipment in the facility so the learning curve to maintain is likely to be low

- Robotic controls have evolved in the recent past and have become much more operator friendly and intuitive. MMCI and FANUC offer training programs for all levels of user interface and operation
Safety
Both eliminate repetitive, heavy lifting and operate safely.

- Lockout keys

- Lockout keys, gates, fence, redundant latching systems, safety sensors, light curtain