Vision Guided Unitizing System Increases Productivity by 30%
The Client & Objective
A global manufacturer of high performance glass products for the building, energy and industrial markets turned to MMCI to design a more efficient solution to their sortation and unitization processes.
The Challenges
This project was inherently complex as the robotic palletizing cell we designed needed to be capable of sorting four different sized blocks that randomly entered the cell and needed to be placed on slip sheets on four different outgoing conveyors. Plus, the abrasive nature of the products being handled provided another challenge. Tests showed that the products would damage the existing belt conveyors if they needed to be moved or shifted much while on the belts.
The Solution
After evaluating the existing processes, MMCI proposed the installation of a vision-guided sorting and unitizing system that would integrate seamlessly with existing equipment and processes at the plant.
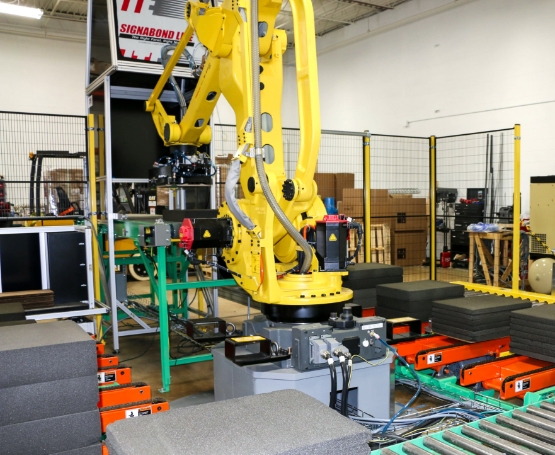
In order to accomplish this, the incoming conveyor was integrated with a vision system to communicate the size, position and location of each block as it traveled down the conveyor.
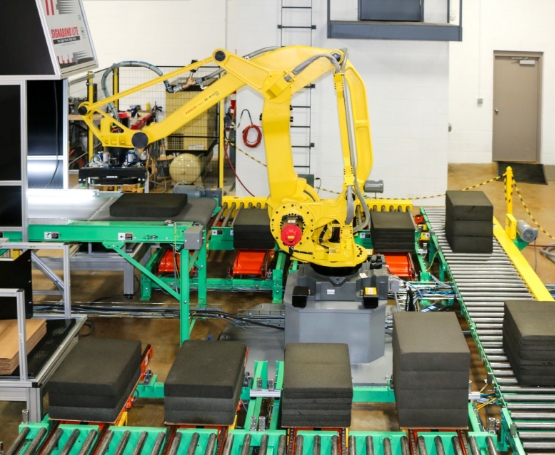
Using this information, the robotic arm was programmed with the ability to locate and grab each block "on the fly" without having to slow down the belt conveyor or incorporate sortation systems to properly align the blocks to be picked up.
The Results
The new solution from MMCI increased sorting efficiency to over 700 units an hour, resulting in a 30% increase in productivity at their plant. Plus, MMCI's controls team was able to integrate the robotic system without modifying existing upstream and downstream processes - providing a turnkey installation with a very fast ROI..