The Re-Engineering of a Bottling Facility
The Client & Objective
Our client, a leading manufacturer of lubricants, faced multiple challenges because their business was growing rapidly and they needed to increase uptime and output. Their 20 year old bottling line was inefficient and breakdowns were causing productivity to suffer. So, they figured they would start by replacing the vintage palletizers – possibly with robotic palletizers.
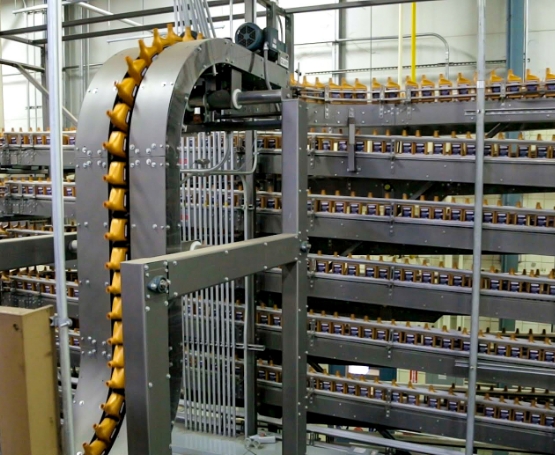
The Challenges
Upon the first visit to the facility, MMCI looked at the entire aging system piece by piece before proceeding with any recommendations. Through a complete material handling study and data analysis, MMCI confirmed that while the palletization equipment was in extensive need of replacement, many opportunities for improvement existed.
The Solution
MMCI automation engineers quickly determined that robotic palletizers were actually not the best equipment for the process, but rather embarked on a plan to integrate high-speed conventional palletizers for their cost-saving advantages and quick payback.
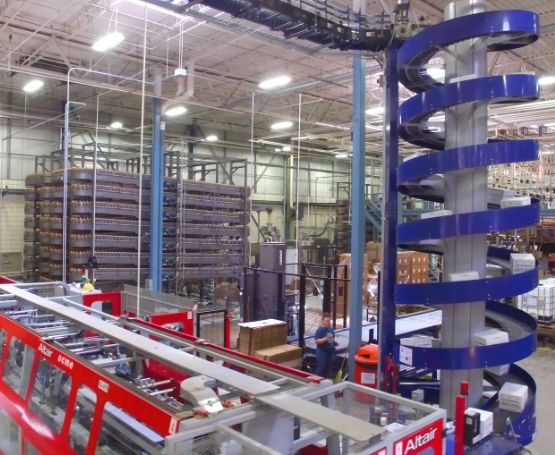
The plan also involved moving the palletizers away from the bottling lines utilizing spiral conveyors and an overhead conveyor system that transferred the cases into the warehouse to reduce congestion near the bottling line and eliminate a significant amount of forklift activity.
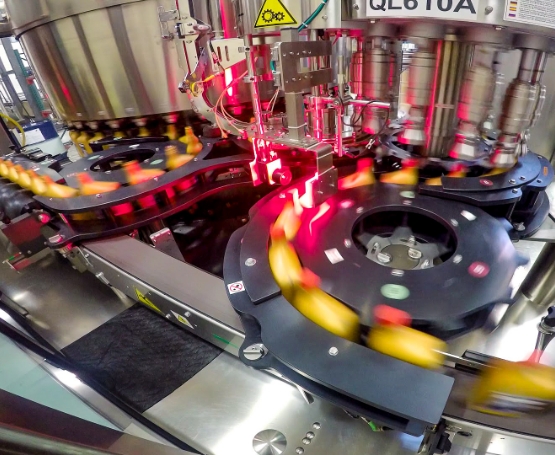
The project also included the enhancement of the vintage filler, case packer, and bottle handling systems. MMCI integrated and networked each piece of equipment in the system to communicate with each other and maximize the throughput of the entire packaging line.
The Results
This custom design and programming by MMCI's engineering team not only created a process that eliminated damage to the conveyors, but it also kept the conveyor speed constant. This allowed for a turnkey installation of the new sortation system without having to modify the existing upstream equipment and processes.