Nu Skin
MMCI Streamlines Nu Skin's Order Picking Process
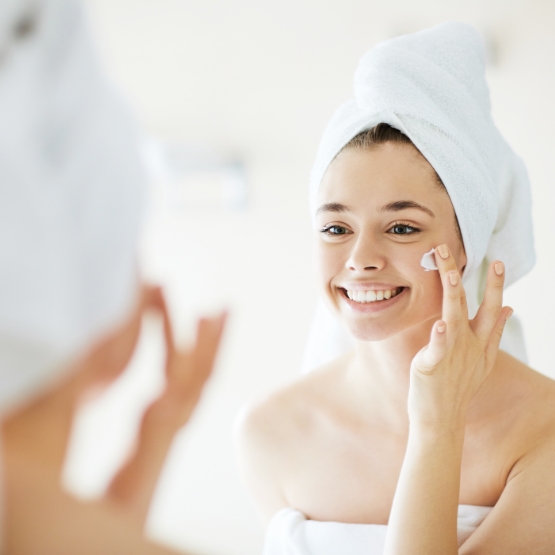
The Client & Objective
Over the past 30 years, Nu Skin has become a leading personal care company by combining products that feature “all of the good, none of the bad” with a mission of becoming the world’s largest direct selling company. Today, the company distributes more than 200 anti-aging products to a customer base across 53 international markets through a global network of independent sales consultants.
The Challenge
Improve the Order Fulfillment Process
Nu Skin not only faced the typical challenges of a fast-growing company, but its Warehouse Management Software from SAP was limiting its ability to utilize alternative picking approaches such as cluster picking and batching in order to improve efficiencies. At the time, all orders were being picked using a discrete picking all method.
Current Situation: Small single
orders cluttered conveyors.
Future Goal: Combine small
orders for more efficient picking.
We needed to change their picking and packing process to:
- Improve productivity
- Relieve conveyor congestion
- Increase order accuracy
- Employ better tools for managing orders and staff
Plus, any solution would need to integrate with SAP and preferably work with the existing pick-to-light technology. Nu Skin management had evaluated the option of having its in-house IT team modify SAP’s software to address these challenges, but the solution proposed by MMCI Order Fulfillment and its DCX Software Suite proved to be much more appealing.
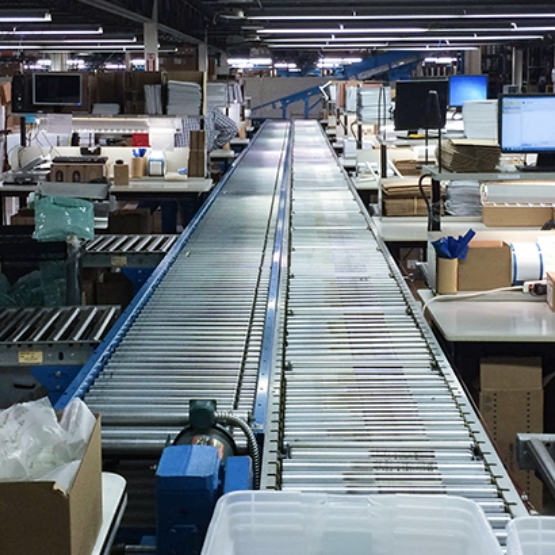
The Solution
After evaluating order profiles, software and existing systems, MMCI determined that Nu Skin could accomplish its goals by introducing batching and cluster picking processes while integrating various modules from the DCX Software Suite to improve the inventory control, order allocation and cubing processes.
The Results
Improved Productivity & Less Conveyor Congestion
By moving Nu-Skin from a discrete picking process to batch picking, we immediately improved picking efficiencies and greatly reduced the number of containers on the pick line.
Then: Each order picked
and put in a tote.
Now: Single items batched, pulled at
one time, and put in a tote.
The DCX Software Suite allowed us to group similar orders into batches that could be deconsolidated in a centralized packout area. It also allowed us to break out the non-conveyable orders (those that shipped in envelopes) to be cluster picked in a separate area using existing pick-to-light technology.
Then: Over 3 miles walked per day
with descrete picking.
Now: Under 1/2 mile walked per day
with batch picking.
This change from discrete picking to batch picking decreased each order picker's "travel time" exponentially. But, we did not stop there. We also implemented DCX Software Suite's Quick Pick module that batched the orders for fast-moving items and placed their inventory in pallet positions near the packout station - allowing them to be "picked quickly."
Increased Order Accuracy
To reduce shipping errors and streamline the quality control process, MMCI integrated DCX Software Suite’s Double Check modules. This technology scans each order as it transfers it over a scale to ensure the weight of the package matches the expected weight of the order and that no special rules apply. “Non-conforming” orders are then sent through the double check process resulting in a fast and efficient quality control system.
1. Double Check for
Quality Assurance
2. Batch Consolidation
3. Packing
With the new systems and DCX Software Suite installed, MMCI was not only able to provide better tools for releasing orders, picking and packing orders, and managing the operation, but it implemented reporting that provided key metrics for managing orders and staffing more efficiently.
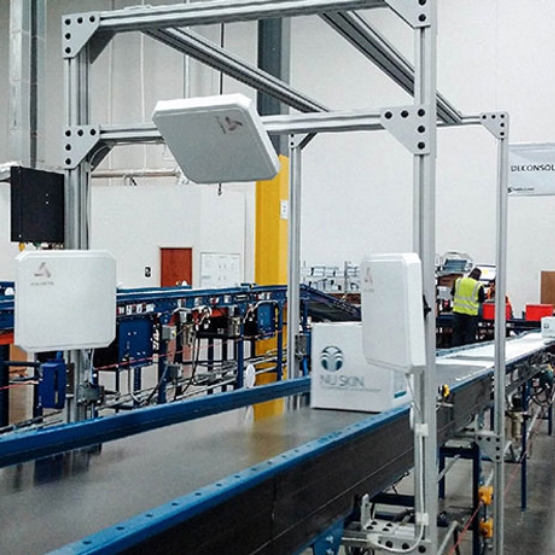
A Long-term Partnership
Nu Skin has now trusted MMCI Automation for more than ten years and the fully modular, expandable and customizable DCX Software Suite has helped increase order fulfillment productivity and reduce costs while providing clear warehouse automation benefits.
As Nu Skin’s trusted partner, MMCI Automation takes pride in creating greater efficiencies in Nu Skin’s existing processes that can withstand continual growth for years to come, providing an endless return on its bottom line.