Concordia Publishing
Rethinking Challenges at Concordia Publishing House
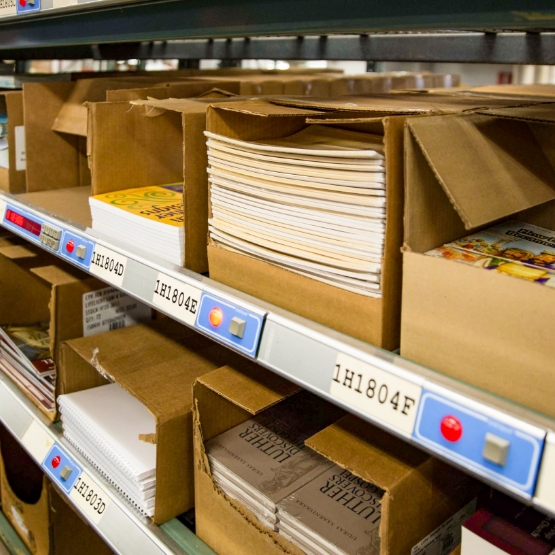
The Client & Objective
For more than 140 years, Concordia Publishing House has been serving individuals, families, and congregations in their proclamation and learning of the Gospel.
Its Midwest distribution center faced strong challenges in response to outdated pick-to-light equipment that was no longer supported by the manufacturer, resulting in a hefty investment needed to replace or update its existing hardware. Needing a replacement solution, Concordia Publishing partnered with MMCI to provide a creative, flexible, and cost-effective solution, that would fulfill its needs for years to come.
The Challenges
A Growing Inventory
Concordia’s SKU count had continually increased over the years as it expanded its product line to better address its customers needs. On an average day, the publishing house processed over 500 orders, warehousing more than 8,000 products. This large number of products required a high-density storage space for its growing number of products, making efficient use of limited warehouse space increasingly crucial.
Inefficient Picking Process
To pick, order pickers were picking discretely into large totes, which often led to congestion on the conveyor system when pack-out operators were unable to keep up with order picking rates. On days when order volume was higher than normal, Concordia had to open additional shipping lanes, requiring additional operators to handle pack-out. Process inefficiencies gradually accumulated and Concordia found itself pushing the day’s orders to the next day more and more frequently.
Outdated Equipment
Its existing pick-to-light equipment, located on case flow racks, was outdated which made finding replacement parts difficult and expensive. In addition to regular part maintenance, each time Concordia added a new SKU, an additional push button was needed for the operator to locate and confirm picks from. The existing pick-to-light system also drove two carousel pods with three carousels each. The carousel controls system was also outdated and difficult to service.
The Solution
MMCI Automation designed, programmed, and installed a smart cart picking system to support order picking. Our Smart Carts provided a significantly cheaper solution, compared to other warehouse management systems (WMS) and technology. The carts, powered by DCX Software Suite, automatically directed pickers through the pick path that was integrated through an iPad on the cart. The iPad utilizes a Bluetooth scanner for location and item verification and eliminates the need for expensive pick-to-light bars on the case flow shelves.
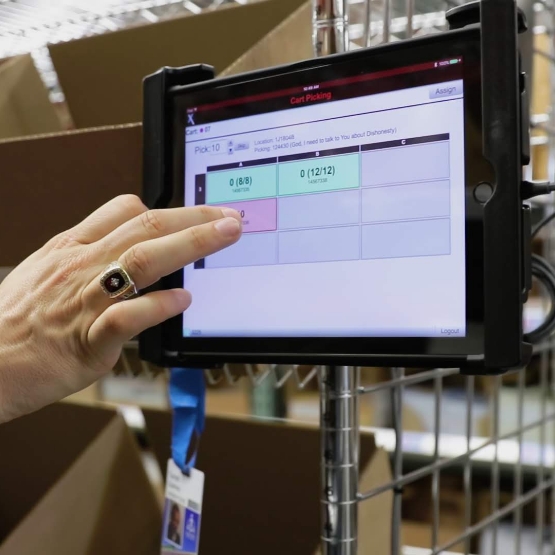
The carts can be configured a few ways (two or three shelves high), depending upon the wave size and box sizes needed. The DCX Software Suite groups containers in waves based upon which aisles are required in order to maximize picking efficiencies on the cart. When a wave of containers is released, the container labels for that wave are automatically printed. An operator will then take the labels and apply them to the correct boxes as determined by the DCX Software Suite's cubing logic and scan each container into a cart slot to begin picking. Pickers are now picking orders directly into their shipping containers, eliminating a step at pack-out and space needed for tote storage.
MMCI Automation also updated the controls system of the carousels and provided DCX Software Suite to drive the carousels. This warehouse automation allows our carts to integrate with carousel and allows picking directly from the carousel into a cart.
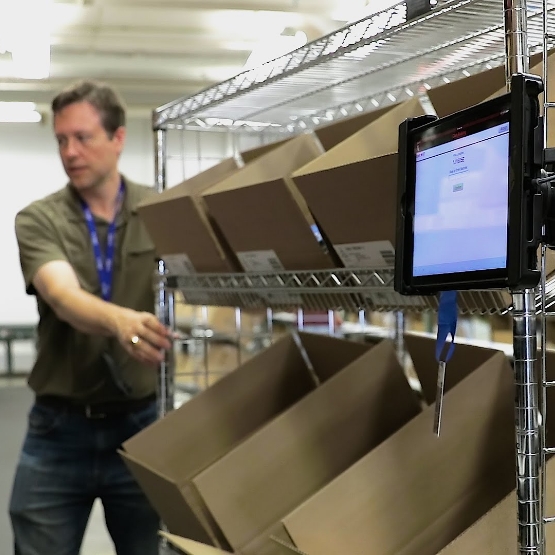
The Results
With our Smart Carts and DCX Software Suite integration, Concordia was able to achieve the same efficiencies at a third of the cost of other WMS solutions. Software and carousel integration through the cart’s iPad eliminated the need for the pick-to-light equipment on the case flow shelves, reducing the resources spent on equipment upkeep. Now, Concordia only needs to worry itself with regular software updates that MMCI Order Fulfillment provides ongoing support for. Picking directly into the box on the cart eliminated a step at pack-out, increasing productivity and helping to reduce wait times and congestion on the conveyor.